
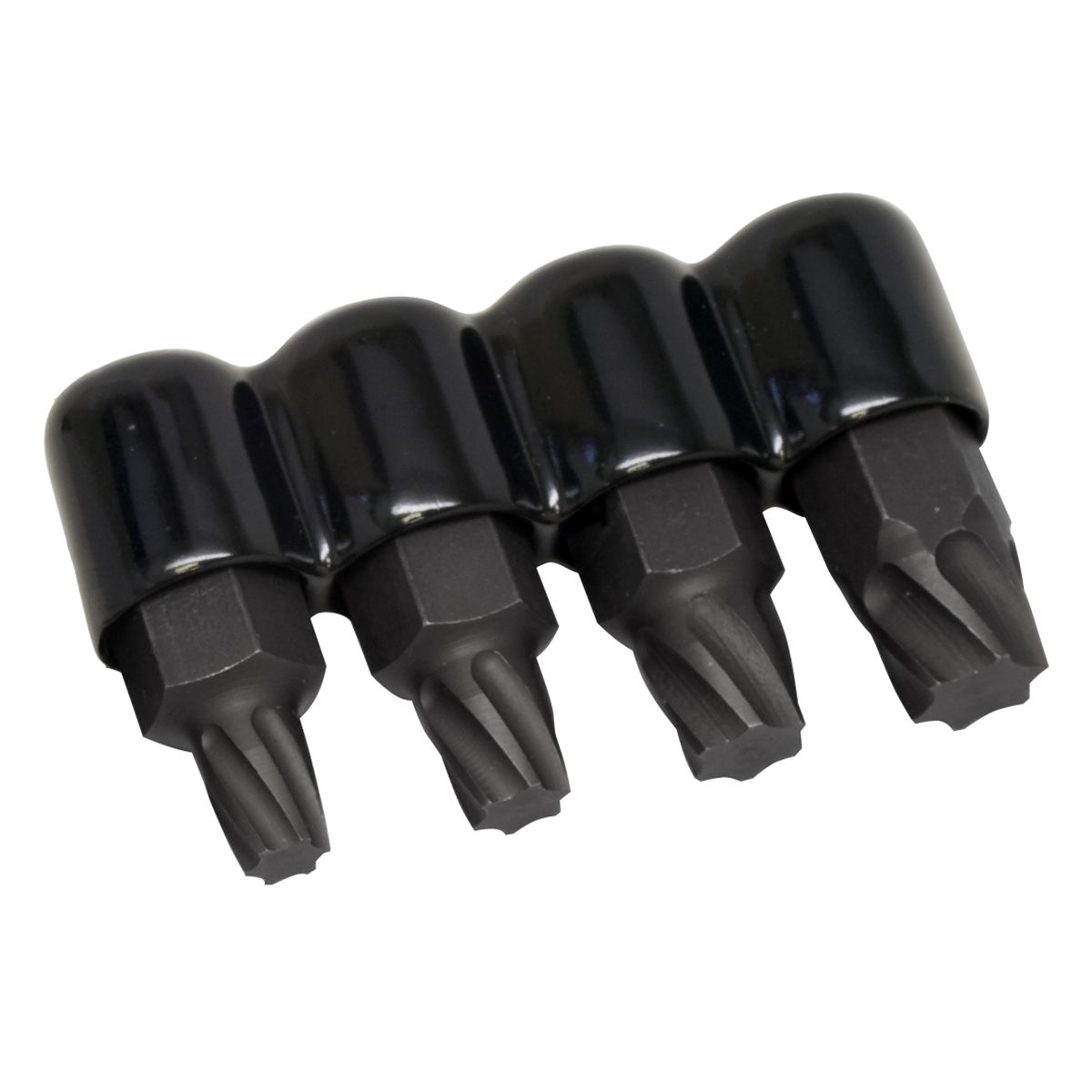
Obviously this method is no good if what you are working on is fragile. If the metal was soft enough to strip in the first place, you will often be able to hammer the screwdriver into the screw head enough to give it a firm position for unscrewing.
#STRIPPED SCREW EXTRACTOR DRIVER#
Depending on how fragile the thing you are working on is, you can also try taking a hammer and tapping your screw driver into the screw.For a minorly stripped screw, this often works. Push down hard and tilt the Phillips at a slight angle and turn. Another simple method is to use a Phillips screw driver that is slightly too big for the hole.If this doesn’t work, combine this method with the rubber band method in step 1. Often there is plenty of grip available for a flat-head screw driver of the right size in a stripped cross-head screw. One of the simplest things to do is if it is a Phillips (cross head) screw, take an appropriately sized flat-head screw driver and, pushing as hard as you can, attempt to remove the screw this way.Once the head is off and the piece is removed, enough of the shaft of the screw should be exposed (assuming you didn’t drill it too deep) now use needle-nose pliers to get the shaft of the screw out.

Try not to drill deeply, you just want to take the head off enough to be able to remove whatever piece you are trying to remove. A slightly more risky method is to carefully drill the head off the screw.Many a time my trusty needle-nose clamping pliers have got me out of a “stripped screw” situation. If you’ve gotten the screw partially up and the head is exposed, get a pair of needle-nose clamping pliers or at the least try a pair of non-clamping needle-nose pliers.Now simply remove as in #5 with a socket wrench. If you are handy at welding and don’t want to wait for the JB Weld to harden, take a nut and place it on the screw then weld the nut to the screw by welding along the inner part of the nut.

Sometimes the rubber will give you the extra grip needed to get that screw out.
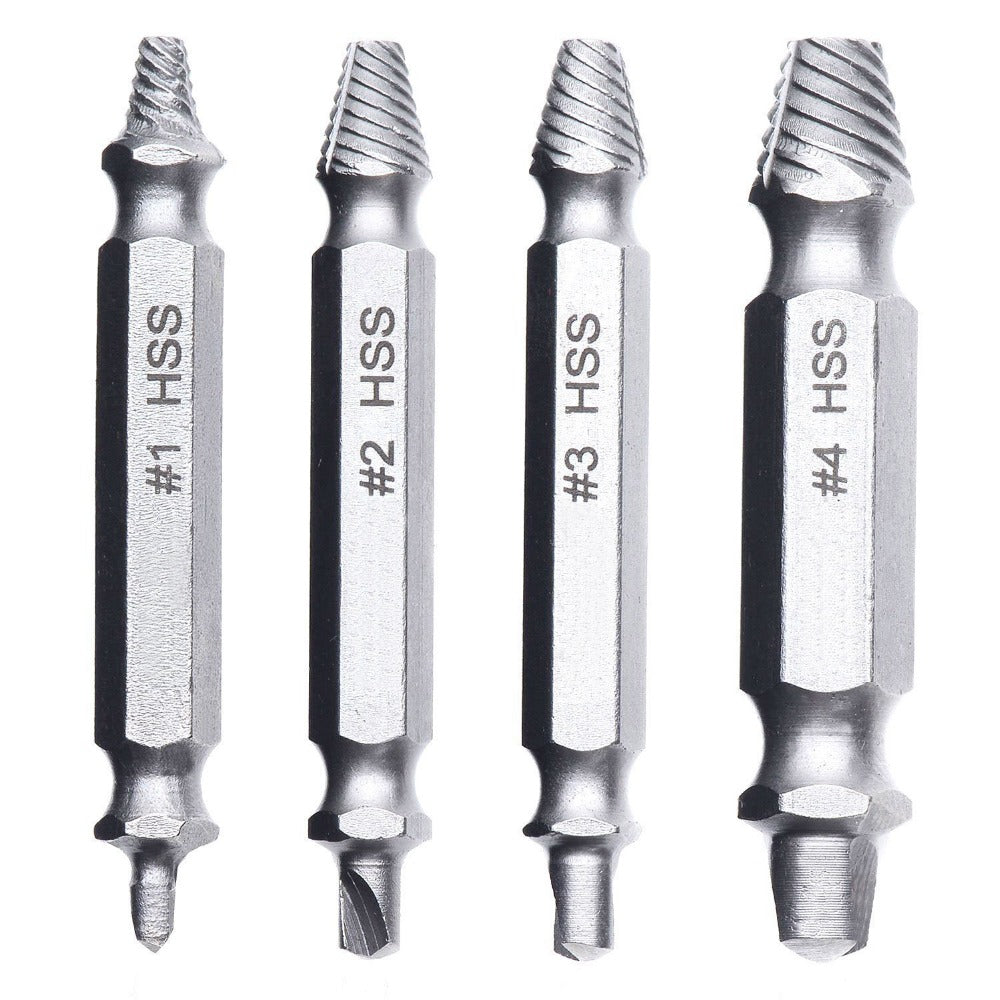
Once it has hardened up, use a socket wrench on the attached nut to remove the screw. If it can’t be flush, use some sort of quick drying temporary gasket or the like to seal around the edges so that the JB weld doesn’t get everywhere, but rather just stays in the hole. If the nut is flush on the screw, this shouldn’t be a problem. Fill the hole with JB weld, being careful to not let it run everywhere. Now place the nut centered on top of the screw. Pick a nut that is about the same size as the screw head or at the least such that the diameter of the hole in the middle of the nut is smaller than the diameter of the hole in the screw. Use JB Weld or equivalently super strong “welding” adhesive to attach a nut to the screw head.They aren’t that expensive and will save you loads of time messing with stripped screws in the future. Works pretty much every time and with very little effort. If you happen to have an “easy-out” screw extractor, this is by far the easiest method.The idea here is just to drill a small hole to allow your Phillips (cross head) screw driver to seat deeper in the hole to help it catch better when you turn it. If you happen to have a drill and some drill bits handy, drill a small hole in the center of the screw.Now take a flat-head screw driver and try and unscrew it using the notch you created. Have a Dremel or equivalent tool? Use the Dremel to cut a notch in the screw head.
#STRIPPED SCREW EXTRACTOR HOW TO#
Now what? You can either A: Think Hammer… really, really big hammer or B: Read the list below and pick the method that seems easiest to you on how to remove a stripped screw or bolt. We’ve all been there trying to void a warranty or otherwise take something apart and you go to take that one last screw off and invariably it strips. Today I found out twelve ways to remove a stripped screw.
